1 铝合金是制造轻型化半挂车的首选材料
时下,能耗和环境污染已成为全球性问题,全社会都在关注汽车的节能减排工作。减轻车辆自重、降低油耗、提高运输效益等措施已是政府、科研单位、车辆制造企业、运输用户普遍关心的问题。铝是仅次于钢铁的第二大金属,铝合金具有一系列优良特性,诸如密度小、质量轻、强度高、弹性好、抗冲击性能好、耐腐蚀、易表面着色、良好的加工成型性以及高的回收再生性等,在汽车工业逐渐得到广泛应用。
随着汽车技术的飞速发展,汽车制造企业在汽车的结构设计、制造技术、材料选用等方面进行了大量的研究工作,希望能够研发出安全可靠、节能环保的新型汽车。而在通常情况下,车身的自重大约会消耗70%的燃油,所以,降低汽车油耗研究的首要问题便是如何使汽车轻型化。使汽车轻型化应首先从材料轻量化入手,这样不但可以减轻车身自重、增加装载质量、降低发动机负载,同时还可以大幅减小底盘部件所受的合力,使整车的操控性、经济性更加出色。而有“轻金属”之称的铝金属,由于其质轻、耐磨、耐腐蚀、弹性好、刚度和强度高、抗冲击性能优、加工成型性好和再生性高等特点,成为了使汽车轻型化的首选材料。铝合金车身汽车也因其节能低耗、安全舒适及相对载重能力强等优点而备受关注。
铝材优点多多:它比钢材轻身,可节省汽车耗油量,并增加载货量;不生锈,回收再用率高;蕴含量及产量多。欧美采用全铝制的重型车已成气候。日常生活中,铝材踪迹处处,这种地球蕴含量第3大最丰富的物质,可造汽车前盖、尾箱、高铁车身,亦会在汽水罐上出现。在有色金属阵营中,是产量冠军,年产量超过铜、铅、锡以及其他有色金属的总和。既有钢的硬度,又有铝的柔韧性,更集传电、传热、轻身、不易生锈的特性于一身。
铝车轻身省油回收有价。由于汽车制造大量采用铝合金使汽车总质量减轻,从而降低了燃油的消耗;由于油耗低、质量轻、汽车的废气排放就少,污染程度就下降。过去几年,铝材增长很厉害,原来我国的车身特重,超载后被罚款,便增加了成本。于是,很多用户买了钢制的货车以后,自己锯掉后面的钢板,换上铝板。这样一来,不仅可以多拉1~2吨货物,而且还不超载,取得了效益。因为铝材重量仅仅只有钢的约1/3,例如一辆5吨的铝制车,比钢制车售价贵8~10万人民币,轻身可增加载货量。铝材回收有价,不比钢材易生锈报废,据说在100年前曾使用的铝材,现在仍有7成在重复使用之中。废旧汽车的回收率高,铝质汽车零件基本上都可回收;回收再生所需要能源少,并且铝可以多次循环再生。因此,无论是在国际上还是在国内,铝合金轻量化车辆将会在未来占领重要舞台。
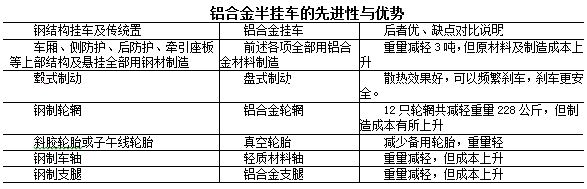
一般交通工具的自体重量每降低10%,燃料开支就可节省8%。因此,铝型材被广泛应用于重卡、船舶和飞机等交通工具,并大大提升了汽车的运动力。一台重5.5吨的铝制半挂车,空载时比非铝制车轻身16%,满载时则可提升运力达3吨。按每辆车每年行驶25万公里计算,每辆增加用铝量2吨,6成满载时间年增运输效益18万元人民币,减碳排放6吨;4成空载时间则年省燃油2400公升。如果按全国市场现有的200万辆来计算,当中的市场效益空间巨大。
全球铝型材行业充满增长机遇。未来5年,中、美、日、印度的汽车业均有稳定增长;中国及欧、美对交通运输领域均有一定投资,这两个因素令全球铝材消耗量大幅增长。
目前我国已成为全球最大的铝型材及铝合金产品消耗国(2009年约590万吨),很多交通运输例如铁路、货车、汽车、航空交通工具,以至机械设备、电力工程均大量需要铝材。单是2011上半年,忠旺铝材国内销售收入同比上升58%。预计到2015年,单单是国内铝压延材的总消耗量将占全球50%(1千万吨)。据悉,忠旺铝材将分4期投放295亿元,积极发展高端铝压延材领域。第一期生产基地完工后,铝压延材产能将达每年180万吨,全数完成后达300万吨。以6.43亿元人民币投得辽宁省盘锦市逾4.4百万平方米生产基地。工业铝型材可透过模具的孔,按客户需求挤压成不同厚度、硬度、抗热度、拉伸度的产品;高精铝压延材即铝板平板状,如可用于交通运输的铝中厚板、易拉罐及机器设备的铝带、电容器的铝箔。忠旺铝材敢拿38亿美金投资新设备,是因为看准铝材市场产值显着上升。我国2010年铝板产量达550万吨,保守预计2015年将增加到1,000万吨,中间450万吨的空白,蕴含无尽商机。忠旺铝材积极投资新机器,准备在已拿下的工业铝型材市场以外,进军高精铝压延材的高技术市场。
2 铝制半挂车已成为实现轻量化的重要途径
全铝半挂车是指除车桥、悬挂装置、牵引装置以外的其他部件全部实现铝制化的半挂车。铝合金材料比钢铁轻得多,铝制半挂车代替钢制半挂车已成为国际上实现轻量化的重要途径。目前我国运行的载重挂车,多用钢铁制成,自身较重,燃油消耗量大(百公里油耗达40~60升),厢式、罐式、平板和集装箱等半挂车一直是公路运输的重要工具,但也是出了名的“油老虎”,实现轻量化,不仅能够直接降低燃油消耗,而且可以明显提高运输效率。
轻量化途径各显其能,同样性能条件下,铝制半挂车整车重量比钢制半挂车平均减重35%~40%。国内外权威机构研究数据和实际使用效果表明:载重车辆自重每减重10%,油耗可降低3.5~6%。以40吨载重挂车自身结构减重3吨为例,在年行驶15万km,空、满载各半,空载百公里油耗25升、满载50升的情况下,取油耗降低率4.8%测算,则每辆挂车每年空载可节省燃油1575升、满载节省燃油3600升/年,累计年可节省燃油5175升、减少二氧化碳排放当量12.93吨。按每升燃油7元、吨公里运费0.4元计算,单车年节省燃油和提升运输效益合计10万元。
全铝半挂车能给用户带来直接的经济效益和社会效益。据介绍,一辆重型钢制半挂车空载时的百公里油耗通常高达25升。只要汽车轻下来,油耗便能降下来。如果每趟运输可以多运送800kg,1年下来将会多运送超过1000t, 尤其在寿命周期内可节油4.5万升,减少二氧化碳排放110吨,所产生的效益是非常可观的。
相关数据统计,目前我国载重挂车(厢式挂车、中重卡挂车、平板挂车)社会保有量约300万辆。虽然占汽车总保有量的比例不高,但其燃油消耗量却占到汽车总消耗量的25%以上。目前,我国汽车燃油消耗量达1.38亿吨,占我国燃油总消耗的40%,其中载重挂车(总质量大于15吨)年燃油消耗量高达4000万吨。如果我国铝制半挂车的应用比例能达到发达国家70%的同等水平,就有210万辆载重挂车是采用示范高效节能铝制挂车,则每年可节约燃油消耗766万吨、减少二氧化碳排放当量2200万吨、增加运输业节省燃油和提升运力效益1780亿元,对推进我国交通运输领域节能减排和转变增长方式具有重大的现实意义。
欧美等发达国家铝制半挂车的开发和应用已有30多年的历史,走在世界前列,技术已相当成熟。目前铝制挂车的普及率已经达70%以上,并向标准化、列车化趋势发展。在德国,自卸(半)挂车的轻量化正开展得如火如荼。几乎所有的自卸挂车制造商都在致力于这方面的改进工作。轻量化成效不言而喻毋庸置疑,对于自卸车而言,有效载荷是其获取利益的最关键的因素之一。在德国,眼下比较流行的自卸半挂车的配置方案是:4×2半挂牵引车+3轴自卸半挂车,这种配置方案得到了越来越多的应用,这种趋势导致其变得更加专业化。位于德国北方下萨克森州的Carnehl公司推出了一种采用半圆形货箱的3轴自卸挂车,自质量仅4350kg。自卸挂车的轻量化成效主要源自在承载着圆形或者箱型料斗的挂车上积极地应用轻金属材料。另外,车轮、空气悬架和底盘车架等也都采取一定的轻量化措施。对于那些尤其是主要从事散装货物运输的企业,如在大型工地运送碎石、沙子和沥青等物品的,这种自卸半挂车的轻量化是十分有意义的。我国铝制挂车的研制尚处于起步阶段,为适应交通运输工具轻量化的需要,我国挂车生产企业与用户做了大量的积极探索和尝试。采取了诸如使用铝轮毂、铝油箱、铝挡板等零部件和真空轮胎、空气悬挂等手段,但这些轻量化的方式都只是局部的、零散的,远不及国外铝制挂车所能达到的效果。
3 采用铝合金制造半挂车的典型零部件
铝在半挂车上的使用呈逐年递增的趋势。局部或整体使用铝材的车型有很多,车身所使用的铝材基本都是合金铝,通过增减合金元素的配比和采用适当的热处理工艺等,使其达到所需性能。目前,用于半挂车车身板材的铝合金主要有Al-Cu-Mg(2000系),Al-Mg(5000系)和Al-Mg-Si(6000系)3种。6000系合金铝由于其可塑性好、强度高,成为许多半挂车生产商的首选新型车身材,料。如欧洲的半挂车生产商一般会使用成型性能较好的6016合金铝作为主要的车身板材;而美国的半挂车生产商则使用具有足够强度的6111合金铝作为车身的主要板材。对于车身的不同部位、不同构件,所使用铝材的合金成分、种类和热处理工艺也并不相同。如车辆的保险杠骨架、加强梁或侧防撞梁等,所使用的铝材都应具有足够的强度和韧度,在发生碰撞时要有良好的吸能特性(比钢板增加50%左右);车辆传动系统使用铝质构件,不但具有足够的强度和韧度,同时还具备良好的导热能力。事实证明,半挂车使用铝材确实取得了良好的社会效益和经济效益。
经过多年的发展,现在半挂车保险杠的结构与以前的保险杠结构相比已经发生了很大的变化二十年前,车辆前后保险杠是以金属材料为主,用厚度为3mm的钢板冲压成U型槽钢,表面处理镀铬,与车架纵梁铆接或焊接在一起,与车身有一段较大的间隙,好像是一件附加上去的部件。
随着汽车工业的发展,半挂车保险杠做为一种重要的安全装置也走向了革新的道路上。今天的半挂车前后保险杠除了保持原有的保护功能外,还要追求与车体造型和谐与统一,追求本身的轻量化。为了达到这种目的,目前前后保险杠兴用了铝合金,人们称为铝合金保险杠。保险杠分为前保险杠和后保险杠,其作用是当汽车受到前、后方向意外的轻度低速冲撞时,缓和冲击力,吸收冲撞的能量,降低汽车的损害,保证乘员的安全。对于一个完善的车身结构而言,由发动机舱和行李舱两个溃缩吸能区,以及车身中部的高强度乘员舱组成。以车身前部结构为例,一般来说,发动机舱作为溃缩区域被分为三级变形区,其中第一级变形区位于发动机舱前部,用于保护行人和降低车辆在低速下碰撞对于车辆的破坏。第二级变形区位于发动机舱中部,即相容区。当两车相撞时,通过这部分变形区的溃缩最大化吸收和分散能量。第三级变形区则靠近发动机舱后部,位于乘员舱之前,最大程度保持乘员舱完整性,也被称为自身保护区。很显然,前保险杠的位置处于第一变形区,保护行人和降低低速碰撞对于车辆的破坏是其主要作用。当车辆发生碰撞时,前保险杠防撞横梁可以将任何形式的偏置和正面碰撞产生的能量尽可能均匀地分布到两个吸能支架上,使能量最大限度均匀地被吸能支架所吸收,并将碰撞力均匀地传递到其他吸能部位。而当汽车在市区道路发生的低速追尾等碰撞时,前保险杠防撞横梁对保护翼子板、散热器、发动机罩和灯具等部件起着一定作用。后保险杠防撞横梁则可以减少行李舱、尾门、后灯组等部位的损害。
如今,汽车轻量化是未来的发展趋势,保险杠也不例外。目前,国际上一些汽车品牌开始使用铝合金材料来制造防撞横梁。钢制保险杠防撞横梁采用提高钢板抗拉强度,从而减小厚度,提高材料吸收能量性能。而铝合金保险杠防撞横梁则是反其道而行之,通过优化结构设计设置不同厚度,从而提高吸能性能。经过合理设计的铝合金保险杠防撞横梁不仅比钢制保险杠防撞横梁更轻,并且能够吸收更大的能量。虽然铝合金保险杠防撞横梁重量更轻,效果更好,但其制造成本比钢制保险杠防撞横梁更高。但随着汽车轻量化的设计逐步发展,铝合金保险杠加强横梁也开始出现在一般车型上。保险杠防撞横梁作为车身结构中相对并不太复杂的组件,铝合金保险杠将很可能代替现有的钢制保险杠。
采用铸铝缸体,可以减轻发动机的重量。从使用来看,铸铝缸体的优势就是重量轻,通过减轻重量实现省油。在同等排量的发动机中,使用铝缸体发动机,能减轻20公斤左右的重量。采用了全铝合金的材质,减轻了车身重量同时,还增强了发动机的散热效果,提高了发动机工作效率,而且寿命也更长。从节油的角度看,铸铝发动机在节油方面的优势颇受人们关注。除了重量上的差别以外,在生产过程中,铸铁缸体和铸铝缸体也有很多不同。铸铁生产线占地面积大,对环境污染大,加工工艺复杂;而铸铝缸体的生产特点恰好相反。从市场竞争的角度来说,铸铝缸体具有一定的优势。铁和铝的物理性能不同,铸铁的缸体热负荷能力更强,在发动机的升功率方面,铸铁的潜力更大。打个比方,一台1.3升排量铸铁发动机的输出功率可以超过70kW,而一台铸铝发动机的输出功率只能达到60kW。据了解,1.5升排量铸铁发动机通过涡轮增压等技术,可以达到2.0升排量发动机的动力要求,而铸铝缸体发动机则很难达到这一要求。企业常说的全铝发动机是指缸盖和缸体都是铝合金制造的发动机。而缸盖是铝合金,缸体是铸铁的发动机,仍被称作为铸铁发动机。但事实上,早在很多年以前,汽车厂家的发动机就已经大规模地采用全铝缸盖了。由于缸盖本身的重量并不大,所以汽车制造商热衷于它并非是由于它的重量轻,而是由于它具有良好的散热性能。随着发动机技术的飞速发展,四气阀结构成为了发动机的主流设计趋势。与两气阀发动机相比,每缸四气阀的气缸盖比每缸两气阀的气缸盖在工作时要产生更多的热量,因此采用全铝缸盖是最好的解决办法。出于成本的考虑,气缸体采用全铝的设计要比气缸盖要晚得多。气缸体是发动机上最重的部分,因而使用铝合金材料可以减轻发动机的重量,从而达到减轻整车重量的目的。
水箱架一般由7个零件构成,改进后的结构将重量从5km多减少到了3km。车身框架前部的纵向支架是分开两片的设计,以便万一前部发生碰撞时维修方便。车身框架的后部是全新的开发成果。因为更为严格的后部碰撞安全法规和空气悬架要求其结构有更大的刚性。一个大型整体铸件与车梁纵向连接,这个铸件同时支撑着车身后部整个的框架。如此高的刚性保证了油箱在车身后部发生碰撞时能够安全正常的使用。车身的前后结构通过顶架、车梁、乘客座位以及底盘架连接在一起,形成了一个整体空间框架。当然,汽车使用铝材也存在一些不足。在生产铝质车身的汽车时,焊接铝质车身比焊接传统钢质车身能耗增加60%。而且一旦发生交通事故,铝质车身的维修费用较高。由于铝材的溶点较低、可修复性差,维修技师需要使用专用铝车身修复工具及特殊的工艺方法进行修复。
目前,我国汽车用油已占全国汽柴油消费的65%,而我国商用车耗油占整个汽车耗油的70%。轻量、节能、环保成为国际汽车工业研究的主题。我国虽为全球第一大铝材生产国和消费国,但铝材应用在交通领域的比例仅占18%,推进铝材在交通领域的应用和汽车轻量化技术势在必行。高效节能全铝挂车产业化及示范应用,是利国利民的大好事,生产企业应不断提升技术水平、持续改进制造工艺,加快示范生产线建设,实现产品结构简单化,部件生产标准化,提高产品专利意识,特别是在示范推广期,要锁定目标用户,实现重点突破。并根据用户需求,在重点企业试点推广,起到引领示范作用,以应大力推动其产业化进程。
(责任编辑:朱竹)